Tomorrow Home
Updated: 16 August 2024
Location: Cornish Park, Lindsay Walk, Spennymoor, County Durham
Developer: Lovell Partnerships
Number of units: 3
Aim(s) of Project: To provide a direct comparison of ASHP against infrared all electric heating systems. It was also built to an interpretation of the anticipated 2025 Future Homes Standards specification and trials various other technologies and sustainable materials to inform future specification.
Construction method: Masonry cavity wall construction
Energy Compliance method: SAP 2012 as built to 2013 Reg's but also assessed using SAP 10.2 and will be ran through the HEM engine
Overheating compliance method: Not required as built to 2013 Reg's pre ADO. This house type passes using the simplified method with mitigation though as the same house type is plotted on later phases of the site being built out to 2021 Reg's.
Construction start: February 2023
Construction finish: September 23 (this was mothballed temporarily and final commissioning and interiors finished June 2024)
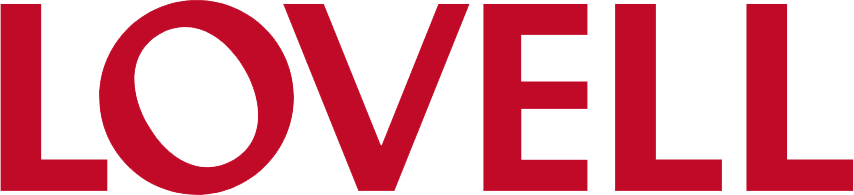
Overview of Project and Specification
In preparation for the new Future Homes Standard, Lovell Partnerships has purpose built two eco-friendly trial homes, called Tomorrow Home, at Cornish Park in Spennymoor. The Tomorrow Home is part of their ongoing commitment to protecting the environment and showcases various cutting-edge technologies designed to cut down on carbon emissions.
In the Tomorrow Home, Lovell are trialing alternative electric heating systems to see which ones are the most reliable, energy-efficient, and affordable. The masonry homes include air source heat pumps (heating and hot water and hot water only), triple-glazed windows, battery storage, waste water heat recovery, infrared heating, EV charging and solar panels. The homes also feature recycled content materials and were painted in low VOC paint to reduce embodied carbon. The results will help inform new, cost-effective housing specifications and support their wider de-carbonisation strategy.
Key learnings
- Specialist sub-contractors who have more knowledge of sustainable technologies had to be brought in to install and commission some of the equipment.
- The infrared radiant heating system was simple to install between the joists and trusses and has a good aesthetic with no radiators required.
- The batteries were installed outside of the plots to mitigate fire risks. However, they were stolen days before the official opening. Consideration will need to be given to security measures. Lovell have since had the new batteries fitted with DataTag and temporary anti-theft barriers installed whilst a more permanent solution is designed.
- Some regions within Lovell have considerable experience of air source heat pumps, although not in the North East. Daikin have provided support and training to our subcontractors and given CPD’s to improve knowledge.
- Waste water heat recovery is now part of the standard Lovell specification for Part L 2021 compliance. It is simple to install and as part of SAP compliance saves on solar panel installation.
- Mechanical ventilation with heat recovery (MVHR) was installed in one unit as a kitchen extraction unit. When compared to conventional MVHR system this minimises the space requirement. MVHR is being increasingly installed where sites have noise or environmental constraints.
- For future projects with MVHR it would be easier to install press-web joists for the ducting rather than I-beams.
- Low VOC paint is difficult to apply, which is especially the case where the paint “cuts-in”.
- Lovell has looked for low embodied carbon materials, but these are often cost prohibitive.